
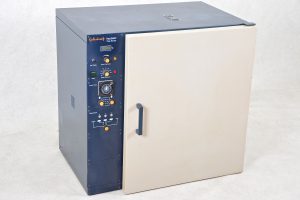
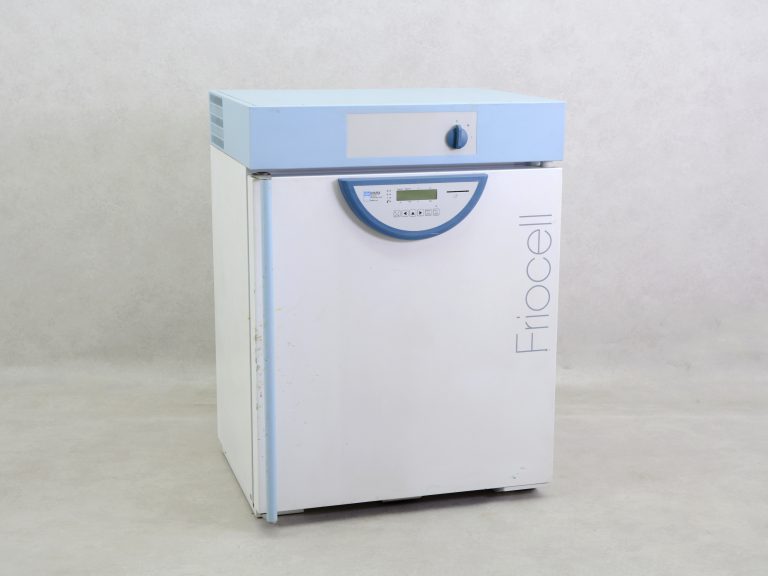
( d) The printout base is raised another 50 μm, and a third layer is exposed. ( c) The printout base is raised 50 μm, and the next layer is exposed, binds to the previous layer and adheres through this to the metal base. Both cured layer surfaces copy the surface textures of the metal and Teflon, respectively. A 50-μm gap between the Teflon surface and the printout base is set, and upon exposure, the far side of the layer sticks to the metal surface of the printout base.
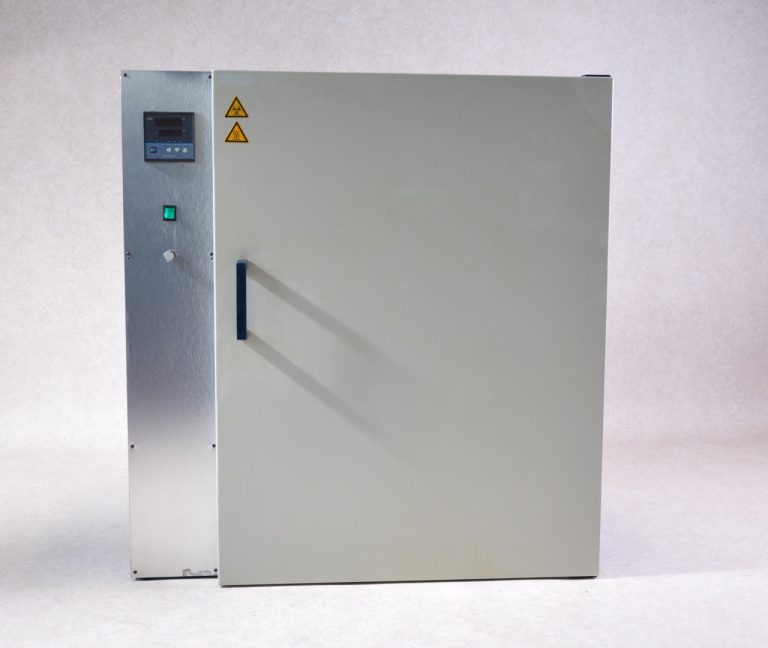
( b) Cross-section of ( a) indicating the first printed layer.
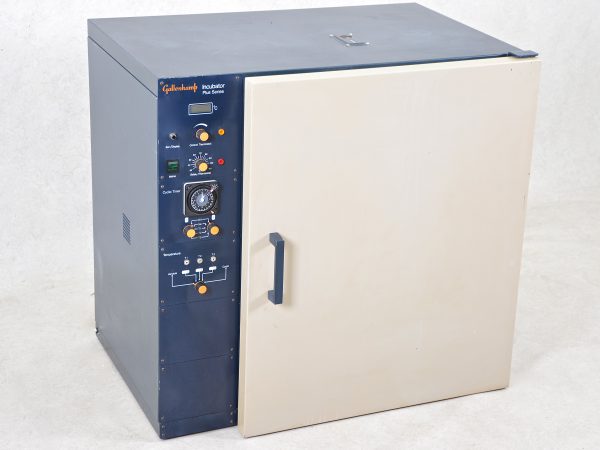
Liquid resin in the tank is confined between the printout base and the tank bottom, which is a transparent Teflon film. The illuminating pattern is provided by a digital micro-mirror device (DMD), which defines the x-y resolution of the UV exposure. ( a) 3D scheme of a generic stereo lithography (SL) printer arrangement. In this case, the layer binds to the previous cured layer, and the process is repeated for subsequent stacking planes ( Figure 1d). In the next step, the base is raised by 50 μm, and a new exposure occurs ( Figure 1c). When the resin is exposed (4 to 10 s, depending on the design), it cures through the gap and adheres to the surface of the metal base, capturing its texture in the printout, whereas the side in contact with the Teflon film does not adhere to the surface, but yet captures its surface texture. Initially, the base is positioned at 50 μm from the Teflon surface, leaving a gap entirely filled with liquid resin ( Figure 1b). Figure 1b,c describes the 3D build-up of the printout. The printout emerges adhered to a metal base that the printer positions in the z-axis at 50-μm resolution. The bottom of this tank is a 127 μm-thick Teflon film (DuPont™ Teflon ® FEP film, Dupont, Wilmington, DE, USA), stretched by contact with a quartz glass (not indicated in the figure). A tank with a transparent bottom holds the printing resin in liquid form. Figure 1a shows the spatial arrangement of the printer parts.
